Стартап в реальном времени. Мобильная молочная кухня. Часть 2
Мобильная молочная кухня: от идеи к конструкции
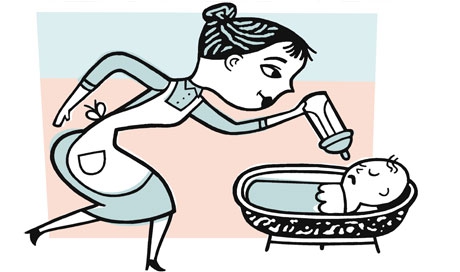
Продолжение. Начало см.
Моя идея, напомню, состояла в том, чтобы сделать систему, которая позволяла бы просто и быстро готовить любое детское питание в любых условиях. Думаете, это просто? Как бы не так. Идее бутылочки с двумя отсеками (для воды и сухой смеси) необходимо было трансформироваться в первые конструкторские разработки. Прошло несколько лет, в течение которых я то забывала об этом проекте, то вспоминала вновь. Это было навязчивой идеей, но поиск технических решений – это не только мое хобби, но и образ мышления. Я часто усовершенствую различные технические устройства дома и в принципе везде, где разрешают.
Как сделать, чтобы смесь высыпалась в отсек с подогретой водой? Вначале была идея с поворотным клапаном из двух пластин: когда одна поворачивается относительно другой, совмещаются отверстия, через которые смесь попадает в воду. Предполагалось, что снизу будет отдельная крышка на резьбе для загрузки смеси. Чтобы засыпать смесь, бутылочку надо перевернуть. Да и при смешивании тоже необходимо перевернуть бутылочку вверх дном, чтобы вся смесь высыпалась в верхний отсек (если посмотреть на рисунок, все станет понятно). После этого надо повернуть клапан обратно и только потом встряхивать. Требовалось продумать, чтобы поворот был на определенное количество градусов, а пластины четко фиксировались друг относительно друга. Был вариант предусмотреть в механизме небольшой совочек, который при повороте выскребает все остатки смеси.
Изначально я планировала делать бутылочку из стекла. Однако выполнить деталь из стекла с полым дном, да еще и с резьбой – не совсем тривиальная задача, мягко говоря. Таким образом, единственным вариантом была пластмасса. Да и теплопроводность более тонкой стенки из пластика выше, чем у толстостенного стекла (в нашем случае это важно, т. к. комплект для мобильного приготовления предполагает питание от аккумуляторной батареи). Как говорят технологи – пластмасса все стерпит.
Я, инженер в области металлургии, пыталась продумывать технологический процесс по аналогии с отливкой деталей из металлов. Однако в литье пластмасс масса тонкостей. Многие детали, которые легко делать из металла, из пластмасс сделать невозможно. Например, стенки с резким переходом по толщине или просто толстостенные детали. Если сплав можно заливать в разрушающиеся формы (песчаные), то с пластмассой все намного сложнее. Следует также учитывать, что каждая дополнительная операция усложняет технологию и увеличивает себестоимость. Анализ этой конструкции показал, что ее довольно трудно создать и еще труднее сделать так, чтобы при повороте всякий раз забивающиеся частички смеси не деформировали и не нарушали герметичность. Конструкция должна быть полностью разборная, удобная для стерилизации.
А если отсек со смесью разместить вверху? Вода должна нагреваться, а значит, на клапан создавалось бы давление, которое могло нарушить герметичность конструкции. При нахождении воды в верхнем отсеке лишний теплый воздух будет выходить через отверстие в соске и специальные зазоры.
У меня было еще несколько вариантов, я обращалась к разным специалистам, которые сначала говорили, что могут спроектировать конструкцию по моим эскизам, но при детальном изучении все отказывались. Некоторые говорили, что на разработку у них уйдет в лучшем случае 6-12 месяцев. Кто-то брался за работу, но потом становилось понятно, что они тянут время, так как у них нет конечного решения.
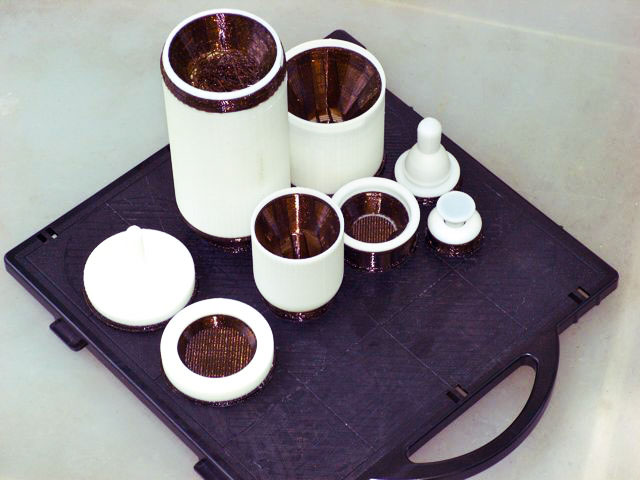
Были варианты и с одноразовым клапаном и с клапаном, который помещается внутрь горлышка. Кстати, этот вариант использован в
Если вода в бутылочке нагрелась, то это не повлияет на полезные качества смеси, т. к. смесь внизу и отделена от воды воздушной подушкой. Максимально в отсек с водой помещается 210 мл, а значит, бутылочка вмещает 250 мл готовой смеси.
Я долго ждала, что кто-то сделает конструкторскую документацию, пыталась обращаться на заводы, где проектируют пресс-формы. Но все в один голос предлагали направить эти работы в Китай или проектировать долго и упорно без гарантий результата. Многие заводы теперь уже не делают пресс-формы, и вообще весь проектный отдел сводится к двум-трем менеджерам, которые формируют заявки, переводят на английский язык и отправляют в Китай.
Поэтому я решила сделать конструкторскую документацию сама, хотя последний раз занималась этим десять лет назад. Я увлеченный человек: после трех бессонных суток у меня был готов весь комплект чертежей из восьми деталей. Модель я отправила по электронной почте в Москву, в ПроЛаб – компанию, занимающуюся созданием прототипов, где мне и напечатали мой первый прототип на 3D-принтере.
18 января 2012